For the creation of any object, manufacturers have developed various possibilities so that the ideal shape can be chosen for the development of the project. Not in all the productions we can see that similar requirements are met for the creation of products, this is how the services that are given in a personalized way arise, to meet all the specifications of each of the clients. Being part of the manufacturing process of any product is not an easy task, since both manufacturers and customers must try to meet all the objectives in order to be accepted by their future customers and users, and these may have certain differences that must find a common ground. One of the aspects that many manufacturers must consider when recreating their clients’ projects is the quantity and quality of each of the objects that they will offer for them.
Why use aluminum machining ?
It is one of those techniques capable of achieving all the goals that are set in low volume manufacturing. For many, low-volume manufacturing seems very similar to other types of manufacturing, but the truth is that it is very difficult to achieve, because, being a very small production, you have to consider many economic aspects, and use the materials very intelligence and care. For this reason, there are not many processes that support low volume manufacturing, because balancing these aspects is a complicated task, however, to the relief of many customers, aluminum CNC machining service.
The aluminum machining is a really effective way to treat this type of materials, since it is capable of creating a perfect piece, without wasting too much material, without molding cost, that is, it will use only what is necessary. The aluminum CNC service is undoubtedly a good strategy to be able to recreate low-volume manufacturing parts, since that interaction between the quantity and the quality of the object that is created is quite good.
The Application for Anodizing Aluminum Parts
As a prototype machining manufacturer, we often encounter that clients request their aluminum parts to be anodized .You’ve probably heard of the anodizing process if you work in the automobile sector or as an architect constructing tall buildings. However, anodizing is primarily utilized in the aerospace and electronics sectors, where specific parts must be ‘corrosion-proofed.’ There are several procedures to which various metals used in those sectors may be subjected. Because anodizing can be used for a wide range of metals, from aluminum to titanium, it is typically the best approach to preserve any particular aluminum surface. Aluminum is the most adaptable of them.
As a result, we’ll go through the essential components of anodizing aluminum pieces. We will discuss sealing anodized CNC machined aluminum parts, sharp dip anodizing, etching, voltage, and time, as well as going through and comparing the many types of anodizing procedures, such as hard coating.
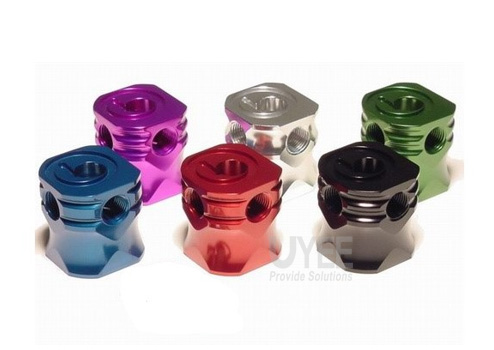
Passivation Process
It is a chemical conversion process that enters the aluminum component and alters its stability. Anodizing creates an exterior barrier of aluminum oxide, which makes the material passive. This coating increases the object’s strength and durability while also protecting its attractiveness.
Anodizing’s Advantages
Electrical and thermal insulation is provided by the most widely utilized anodic oxidation coatings in industrial anodizing. Compared to applying paint to bare metals, the technique enhances the adherence of paint primers and glues. It’s also great for avoiding the galling of threaded components, which is a type of wear produced by adhesion between two moving surfaces.
Rectifiers, Chillers, and Process Equipment
If you’re wondering what type of equipment is required to complete the anodizing process, you might be surprised to learn that there are tiny anodizing kits designed for in-home usage. However, these “anodized aluminum at-home kits” are intended for relatively modest tasks, and they still need extensive knowledge to assure safe application. Several automated anodizing tanks for aluminum anodizing can be used in the apparatus.
Chillers
During the anodizing process, a significant amount of heat is generated. To effectively anodize a part, that heat must be removed, which implies that necessary procedures must be put in place to keep temperatures at an ideal level. Chillers are utilized to level out the metallic oxide deposition, and either water or air chillers aid in the chilling process. The temperature is regulated by using sensors to detect and valves to control it.
Voltage and timing
In two minutes, the technique is explained by Larry Chesterfield’s two-minute read on anodizing current density versus voltage. He provides a few mathematical calculations to assist you in calculating the appropriate voltage and duration to be utilized in proportion to the size of the object being anodized. It may anticipate the time required to produce the desired coating thickness if the current is fixed during the anodized cycle.
Makeup as a Solution
Anodizing aluminum is a labor-intensive process that requires the use of chemical baths and large equipment. Before commencing the procedure, determine the number of liters or gallons of solution required, considering the recommended acid-to-bath ratio (15 percent to 18 percent).
The Oxide Coating Structure
The anodic oxide structure is formed by the aluminum substrate and is fully composed of aluminum oxide. The aluminum atoms are progressively removed from the metal’s surface while the aluminum portion is submerged in the chemical bath, and a current is sent through it.
Pore Composition
The thickness of the aluminum oxide coating layer depends on the voltage applied to the bath and the amount of time the item is submerged in it. Higher voltage accelerates oxidation, and the time of the process influences the coating. Temperature and electrolyte properties, such as temperature and pressure, impact the dissolution rate of the metal surface.
Anodizing Varieties
One (Type II) is commonly referred to as’ regular ‘anodizing, while the other (Type III) is referred to as’ hard ‘anodizing. So, what happened to Type I, and are there any more processes that aren’t covered by the initial classification? We’re here to help you break things down equally and make them more understandable.
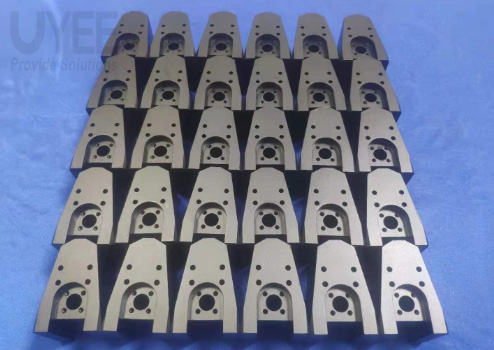
A cost-effective production process
During the low-volume machining process, keep in mind that the end product will be in your hands in no time, as the machines are very precise and fast when milling and turning. Aluminum machining simply takes care of “sculpting” the part until it is able to take the desired shape. The most convenient thing about this type of low-volume production through machining is that the delivery time is very fast, a lot of raw material is saved, and it is possible to work even with the piece that comes from a very complex design. For custom aluminum machining pieces there are no limitations, since the machines are really effective when creating parts, removing all products from any margin of error that may exist, creating parts that were previously believed impossible, and making the dream come true from any manufacturer, even if it is a very small project. If this is the process you need to start your business, go to an expert manufacturer, who can intelligently process your requests, and who is capable of giving you an excellent result, no matter how complex the creation of the parts.
Creation of parts from the service of CNC aluminum machining
Not all companies are capable of developing the ability to create efficient protocols related to the creation of aluminum parts, either in very large batches, or simply in a single prototype. However, to everyone’s relief, companies like UYEE have found the perfect formula to realize the ideas of all their customers, always ensuring the quality of all the objects they manufacture. From aluminum prototype CNC machined to small batch production request . These types of companies apply aluminum CNC machining, and achieve the creation of customized low-volume parts without problems, since within their manufacturing parameters are techniques derived from machining, such as milling and turning. Starting with a small piece of metal, or rather, the most convenient size for this task, the machines begin to do their work with productive and efficient way .
Conclusion
Today ,custom low volume aluminum parts through by CNC machining is sorely welcomed due to client’s requirements on the quantity ,tolerances ,lead time, finish of diversity. Plus , aluminum is the most widely used metal material in the world .So it will still be a big trend in the future development. If you’d like to check out more about the benefits of aluminum machining and rapid manufacturing service, please get in touch with: info@uyee-rapidprototype.com